McIntosh Ustalığı
Bir McIntosh yapmak için ne gerekir?
Deneyim. Tutku. Ustalık.
McIntosh'taki yetenekli bireyler, dünyadaki en kaliteli ev audio ürünlerini tasarlamaya ve inşa etmeye kendini adamıştır. 70 yılı aşkın deneyimimizde, McIntosh kalite ses reprodüksiyonunu tanımlamış ve performans, güvenilirlik ve servis için standart belirlemiştir.
Yeni bir McIntosh modelinin, başlangıç konseptinden nihai ürüne geçmesi aylar veya hatta yıllar alır. Bu süreçte, titizlikle mühendislik çalışması yapılır ve sürekli olarak geliştirilir, ta ki bizim titiz standartlarımıza uyana kadar. Sonrasında, çalışanlarımızın ustalığı, o tasarımları saygın ev audio ürünlerine dönüştürmek için geniş üretim yeteneklerimizle birleştirilir.
Bir McIntosh'un nasıl yapıldığını görmek için aşağı kaydırın.
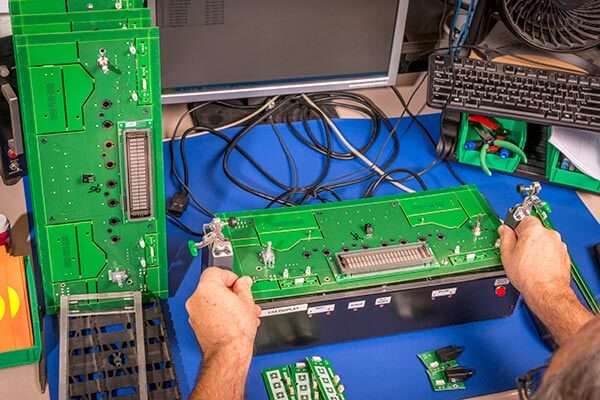
Aylık 7,000'e kadar PCB üretebiliyoruz ve bunlardan bazıları 1,000'den fazla bileşene sahip. Ürünlerimizin ömrünü uzatmaya yardımcı olmak için, her PCB bir üniteye monte edilmeden önce tek tek test edilmektedir. Test için, her PCB, o PCB için özel olarak tasarlanmış bir test düzeneğine yerleştirilir ve detaylı bir bilgisayar test prosedüründen geçirilir; ayrıca çeşitli test ekipmanları ile manuel olarak incelenir.
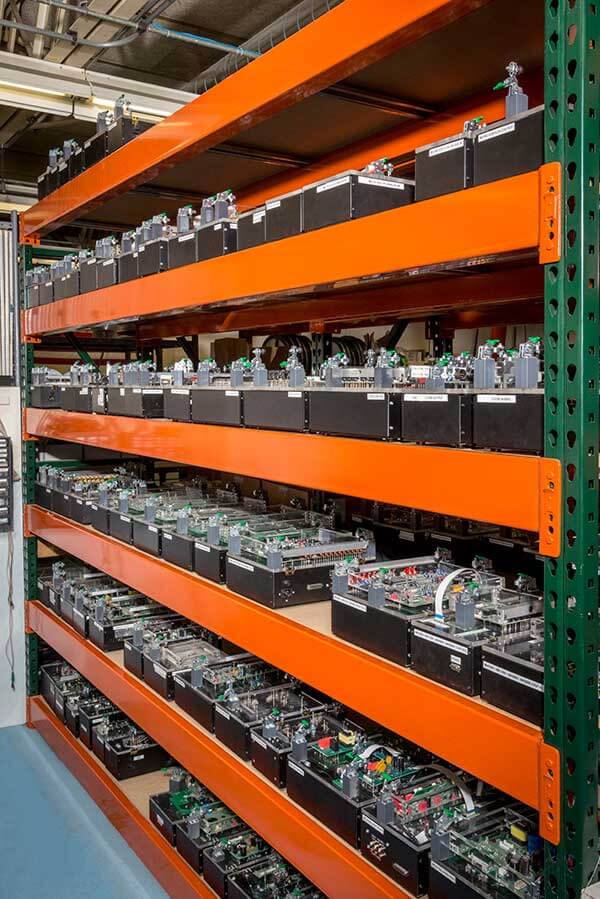
Tüm PCB test düzeneğimiz ev yapımıdır. İşte PCB test departmanımızdaki test düzeneğinin küçük bir örneği.
-
Tüm cam panellerimizi yüksek basınçlı su jetleri ile kesiyoruz. Ürünlerimizde 1/8" – 1/2" kalınlığında cam kullanıyoruz, ancak kalınlık ne olursa olsun, kesme prosedürü aynıdır. Su jetimiz, hassas kesimler üretmek için Bilgisayar Sayısal Kontrol (CNC) ile kontrol edilmektedir.
-
Kesim ucundan su neredeyse 50,000 PSI basınçla çıkar. Bu yüksek basınçta, su jetinin düzgün kesimler yapabilmesi mümkün değildir.
-
Düzgün kesimler elde etmek için, su akışına garnet tozu, bir aşındırıcı mineral ekliyoruz. Yüksek basınçlı su ve garnetin birleşimi, düzgün ve hassas kesimler üretir.
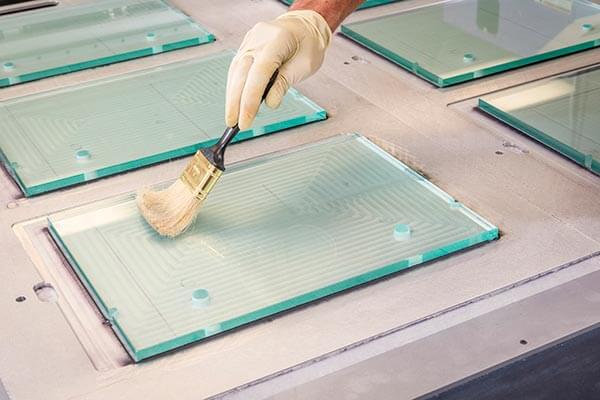
Cam paneller kesildikten sonra, bir sonraki adım olarak onlara McIntosh'un imza "siyah ön panel" görünümünü uyguluyoruz.
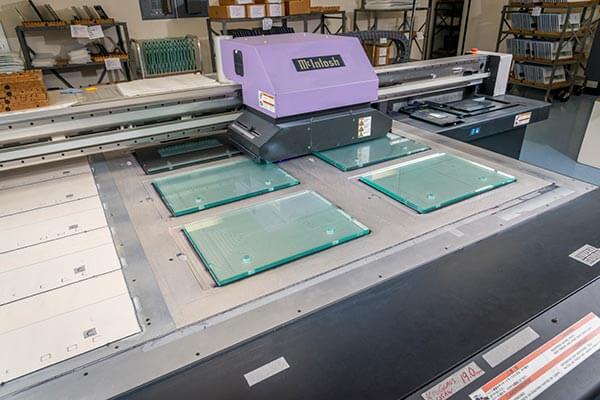
2018'den beri, bu, 1950'lerin sonlarından beri kullanılan ipek baskı sürecini değiştiren özel bir baskı tekniği ile yapılmaktadır.
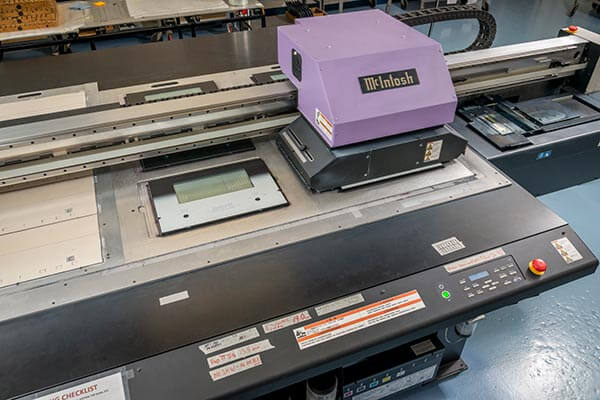
Özel cam tedarikçisi Corning, Inc. ile danışmanlık yaptık ve cam üzerine baskı yapma sürecini öğrenmek için 165 yılı aşkın deneyimlerinden yararlandık.
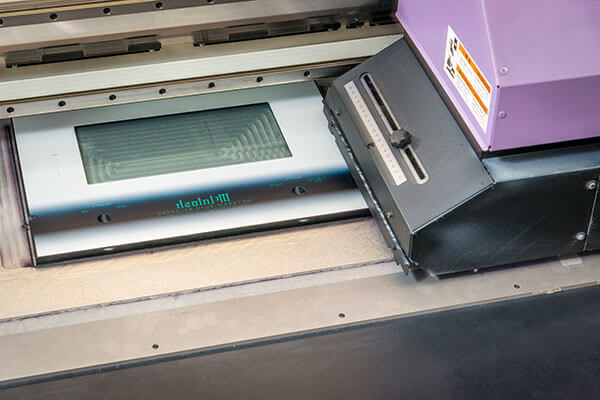
Buradan, istenilen renk yoğunluğunu ve şeffaflığı oluşturmak için çok katmanlı özel UV baskı sürecimizi geliştirdik.
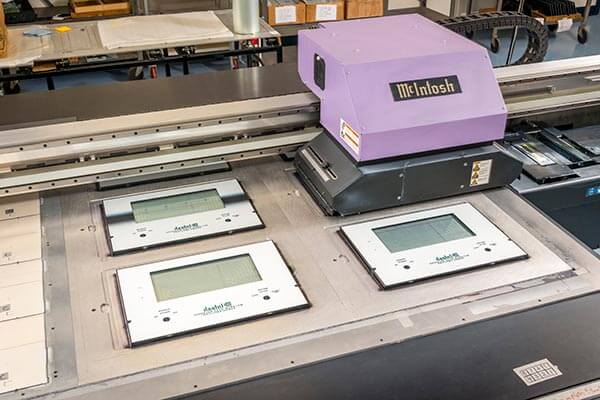
Örnekler, baskının on yıllar boyunca dayanmasını sağlamak için Binghamton Üniversitesi'ndeki Thomas J. Watson Mühendislik ve Uygulamalı Bilimler Okulu'nda simüle edilmiş sıcaklık ve nem koşullarında kapsamlı güvenilirlik testlerinden geçti.
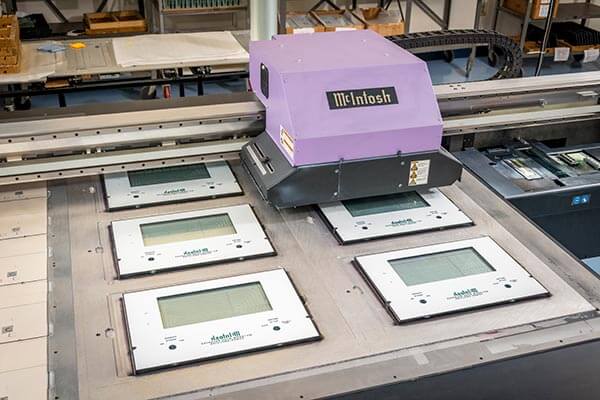
Eski ipek baskı sürecinde olduğu gibi, baskı camın arka tarafında yapılır; böylece birim yıllar boyunca kullanıldıkça ve temizlendikçe, baskı asla silinmeyecek veya okunamaz hale gelmeyecektir.
-
Baskı süreci tamamlandıktan sonra, cam paneller ön panel montajlarına dönüştürülür.
-
Butonlar, contalar ve ölçümlere tescilli mavi parıltıyı veren mavi filtreler eklenir.
-
Tamamlanmış cam panel daha sonra bir metal ekstrüzyona yerleştirilir, böylece birime bağlanabilir.
-
Tüm Autoformer veya Unity Coupled Circuit çıkış trafosu bir metal kutuya yerleştirilir ve genellikle "katran" olarak bilinen 450° F (232° C) özel bir sıvı asfalt karışımına "potlanır." Bu potlama işlemi sayesinde, metal laminasyonlardan kaynaklanan gürültü oluşturan titreşimler etkili bir şekilde ortadan kaldırılır; ayrıca potlama, trafoyu şasiye mekanik olarak izole ederek gürültüyü daha da azaltmaya yardımcı olur.
-
Çoğu trafoda, sadece kablo uçları açıkta bırakılırken, tüm EI çekirdeği katranın içine kaplanır.
-
Potlanmayı bekleyen bir grup Autoformer.
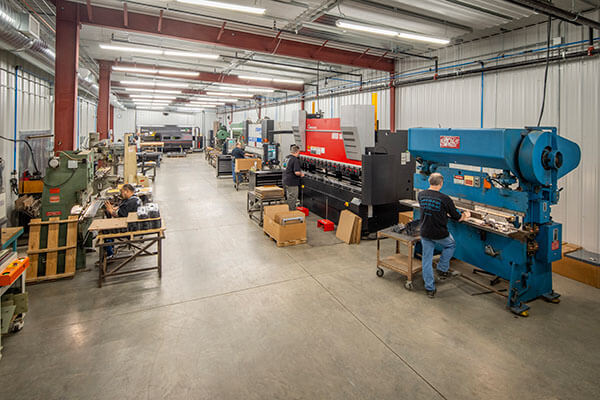
Şasilerimizi, braketlerimizi ve birçok diğer parçayı metal atölyemizde üretiyoruz. 2022 yılında, mevcut alanımıza sığmadığımız için fabrikamıza 4.700 ft2 (436 m2) büyüklüğünde yeni bir metal atölyesi ekledik. Yeni, daha büyük metal atölyesi, kapasiteyi artırmak için iki yeni makine eklememize de olanak sağladı.
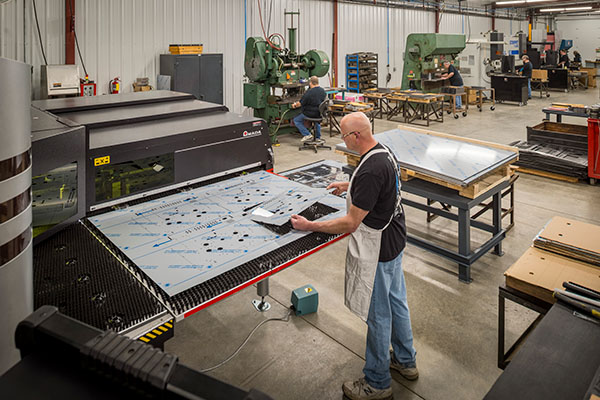
Tüm şasilerimiz, düz çelik levhalar olarak başlar. Düz levhaları ürünlerimiz için gereken şekil ve boyutlara dönüştürmek için CNC Punch Press'ler, Press Brake'ler, bir nokta kaynak makinesi ve diğer ekipmanlar ve aletler kullanıyoruz.
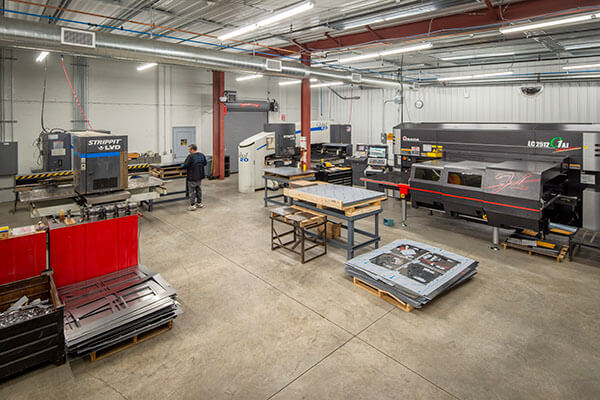
Bu üretim süreci, hem cilalı paslanmaz çelik şasilerimiz hem de soğuk haddelenmiş çelik şasilerimiz için aynıdır, ki bu şasiler daha sonra boya atölyemizde toz boya ile boyanır.
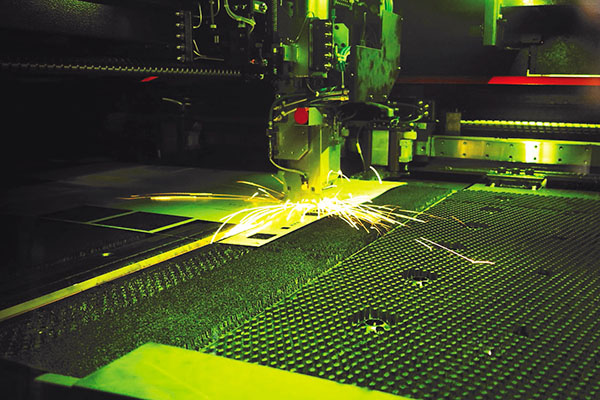
CNC Punch Press makinelerimizden biri, daha karmaşık şasiler yapılırken kullanılmak üzere yerleşik Fiber Lazer kesim yeteneklerine sahiptir.
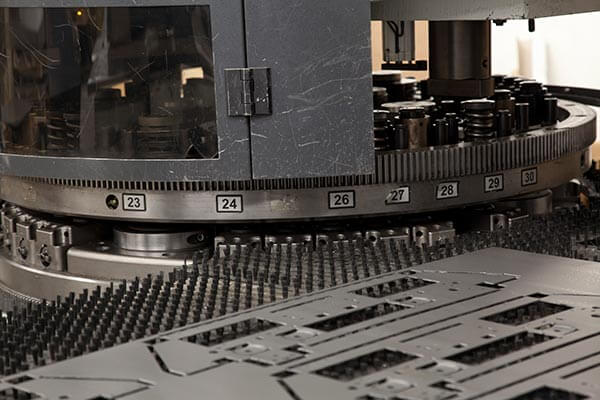
30 istasyonlu Çok Amaçlı Taret (MPT) bulunan Punch Press makinelerimizden biri, şasi yapmak için gereken çeşitli şekil ve boyutları delerek çıkarır.
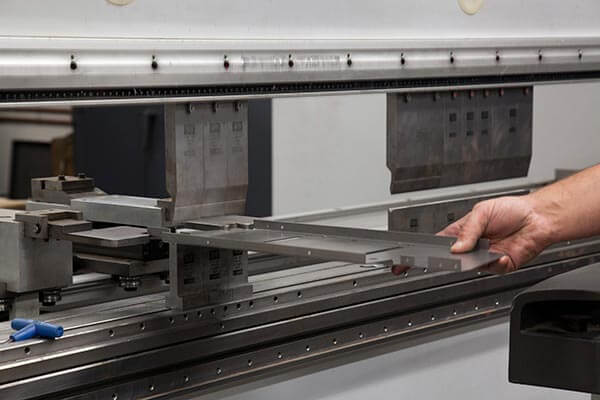
Bir Press Brake, delikli çelik parçaları şekillendirilmiş bir şasiye dönüştürmek için 110 tona kadar kuvvet uygular.
-
Siyah boyalı yüzeyle kaplanan şasi parçaları, 2019'da kurulan son teknoloji toz boya hattımızdan geçtikleri Boya Departmanımıza gider. Parçalar bir konveyöre asılır ve tüm boya hattı boyunca yaklaşık 400 feet (121 metre) yol alır.
-
Parçalar önce boyanın yapışmasını engelleyecek kalıntıları gidermek için kimyasal olarak yıkanır, ardından 380°F (193°C) sıcaklıkta bir fırından geçerek kurutulur.
-
Sonra, her parçaya el ile toz boya püskürtüldüğü manuel boya kabinine giderler.
-
Oradan, boyanın pişirilip sabitlendiği fırına geri gönderilirler.
-
Bu sertleştirme işlemi sırasında parçalar, kurutma döngüsüne kıyasla fırında yaklaşık 4 kat daha uzun süre kalır.
-
Tüm bireysel parçalar ve alt montajlar (PCB'ler, Otomatik Transformatörler, cam paneller, şasiler vb.) yapıldıktan sonra, bitmiş ünitelerin monte edildiği Montaj Bölümüne gönderilirler.
-
Burada, yetenekli zanaatkarlar tüm bu ayrı parçaları alıp işlevsel üniteler haline getirirler.
-
Montaj hattında üretimin çeşitli aşamalarında olan ürünler.
-
Son testlerini geçtikten sonra, ünitelerin kalan tüm parçaları monte edilir.
-
Buna ön panel montajı da dahildir.
-
Her bir metre, ticari markalı mavi rengimize kalibre edilmiştir, böylece tüm metreler aynı görünüme sahiptir. Bu, zamanla ev ses sisteminize farklı parçalar ekledikçe, üniform bir görünüm sağlanmasına yardımcı olur.
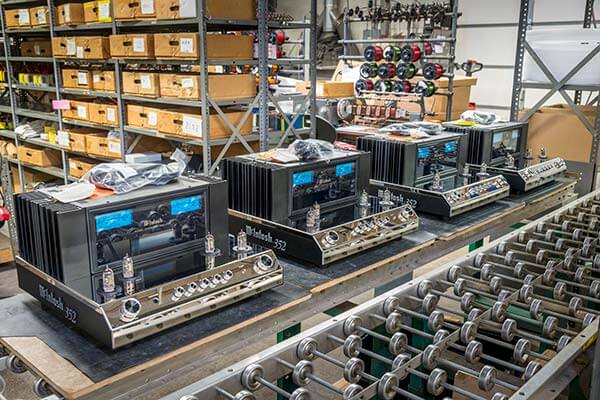
Paketlenmeyi bekleyen üniteler. Üniteler temizlenir, cilalanır, bir torbaya konur ve Mühendislik Departmanımızın tasarladığı dayanıklı nakliye kutularına yerleştirilir.
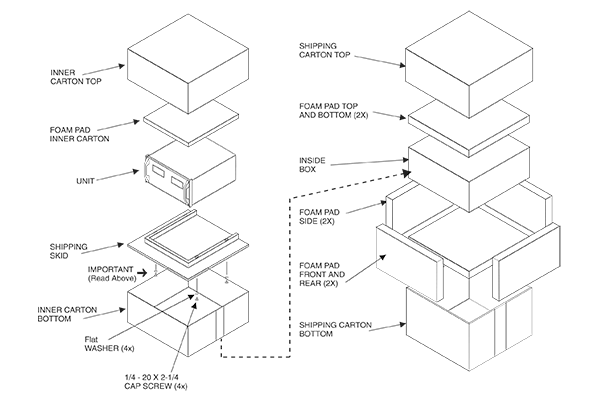
Çoğu ürünümüz "kutunun içinde kutu" tasarımına sahip olup, özel köpük malzemeleri ürünleri yerinde tutar ve zarar görmelerini önler. Bazı ürünler paketlenmeden önce ahşap bir nakliye paletine sabitlenir. Tüm bunlar, kutuyu açtığınızda sizi kusursuz bir üniteyle karşılamak için yapılır.
-
Mühendislik Departmanımız, çeşitli test yeteneklerine ve özel ekipmanlara sahiptir. Bunlar arasında zemini asılı büyük bir Yankısız Oda da bulunmaktadır. Bu oda, tüm sesleri emer. Burada, bir ürünün akustik özelliklerini yankı, yansıma veya çınlama olmadan test edebiliriz, bu da test sonuçlarını etkilemez.
-
McIntosh hoparlör XR1051, yaklaşık 1984 yılında uzun süredir Akustik Mühendis olan Carl Van Gelder tarafından Yankısız Odamızda test ediliyor. Ayrıca, özel Yankı Odası'nda bir ürünün akustik gücünü ölçebiliyoruz.
-
Ayrıca büyük bir Elektromanyetik Uyumluluk (EMC) Odası'na sahibiz.
-
EMC odasını, ürünlerimizin diğer elektronik cihazları etkileyebilecek elektromanyetik sinyaller yaymasını test etmek ve ayrıca diğer cihazların yaydığı elektromanyetik sinyallerin ürünlerimizi nasıl etkilediğini test etmek için kullanıyoruz.
-
Bu özel test alanlarının yanı sıra, mühendislerimiz McIntosh ürünlerini tasarlarken çeşitli özel test ekipmanları kullanır. Tabii ki, en özel dinleme ekipmanı insan kulağıdır ve bu da Mühendislik binamızdaki özel dinleme odasında kapsamlı bir şekilde kullanılır.
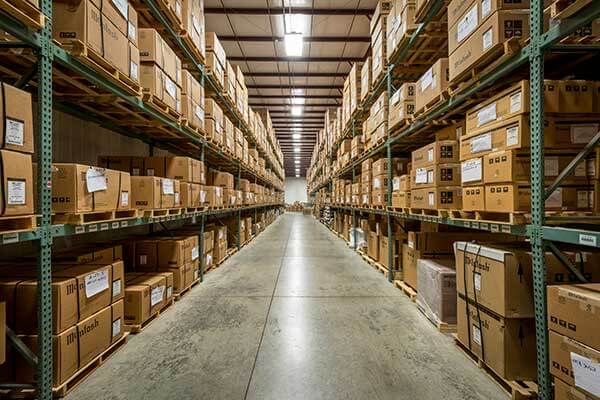
22,000 ft2 (2,043 m2) büyüklüğünde, hem hammadde hem de bitmiş ürünlerin güvenli bir şekilde saklanabildiği büyük bir depoya sahibiz.
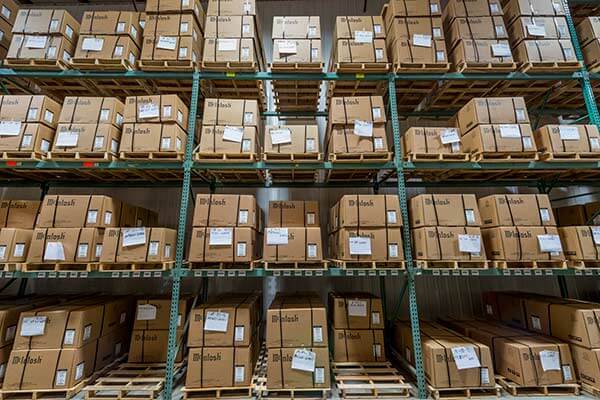
Buradan ürünlerimiz bayilerimize ve dünya çapındaki distribütörlerimize gönderilmeye hazır hale gelir.